Logistics Business magazine, together with the Information Factory, have produced a new 8 page digital magazine on logistics cost allocation: how to calculate and allocate costs in logistics operations. Editor Peter MacLeod talks to iFactory CEO Robert Jordan to understand how transport and distribution businesses can use a tool that accurately determines costs. Learn how to drive revenue and boost profits in logistics.
Read the free eBook here.
From Black Box to Industry-Leading Solution
A few years ago, The Information Factory produced a Cost Allocation Tool for DHL Express that today is deployed globally by the renowned logistics and courier company. It has now been developed into a tool suitable for the broader logistics sector: LogiCAT has the potential to offer users a true competitive advantage.
Operating in a commercial landscape with these wafer-thin margins means that understanding the true cost of operations has never been more critical. Yet, somehow, many organisations still seem to be operating with only limited visibility into their actual costs, relying on aggregated figures and educated guesswork that can often fail to inspire confidence among decision-makers, finance departments or those in customer-facing roles who need to know how much they have to play with when neck-deep in negotiations with a client.
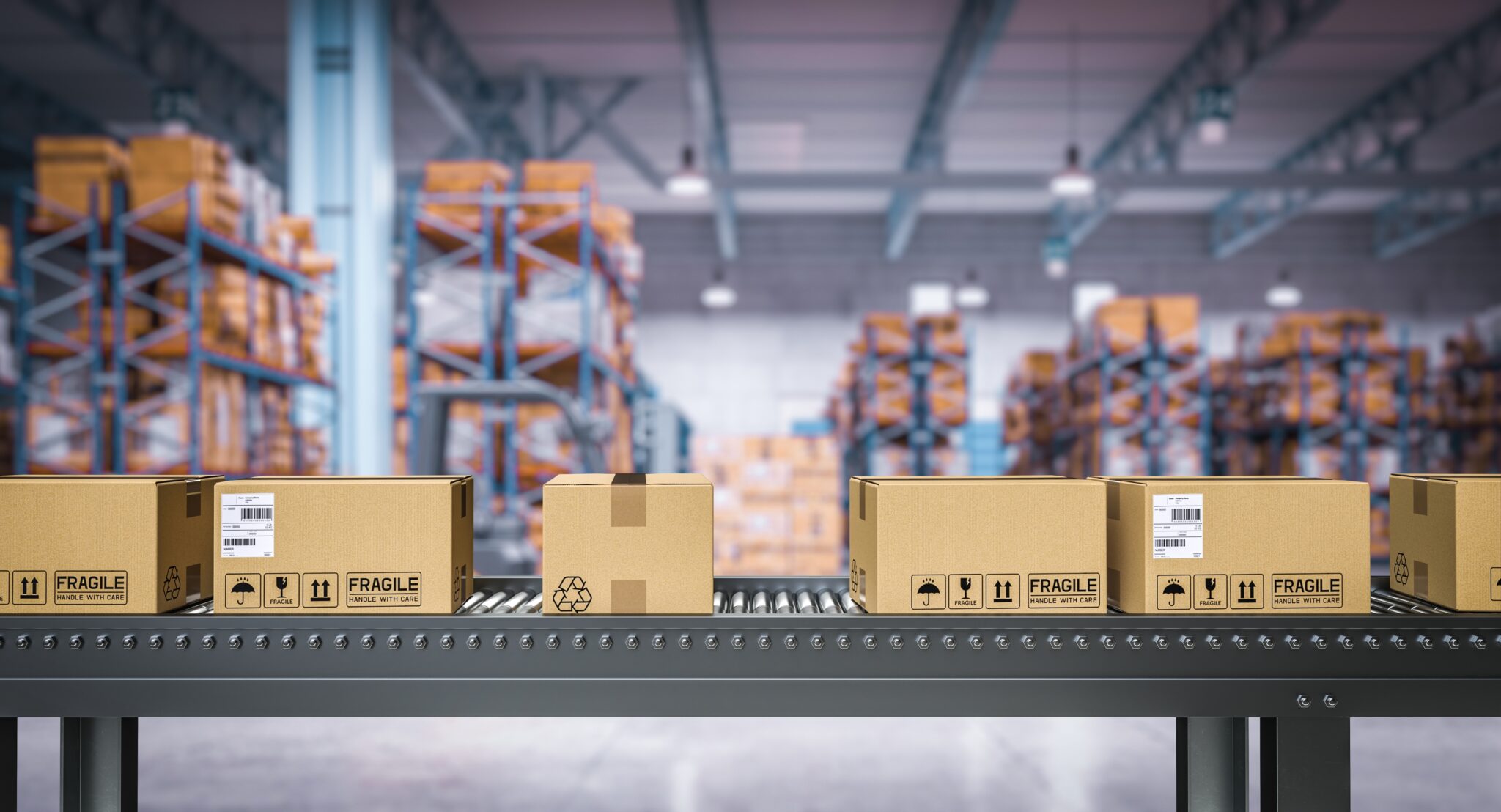
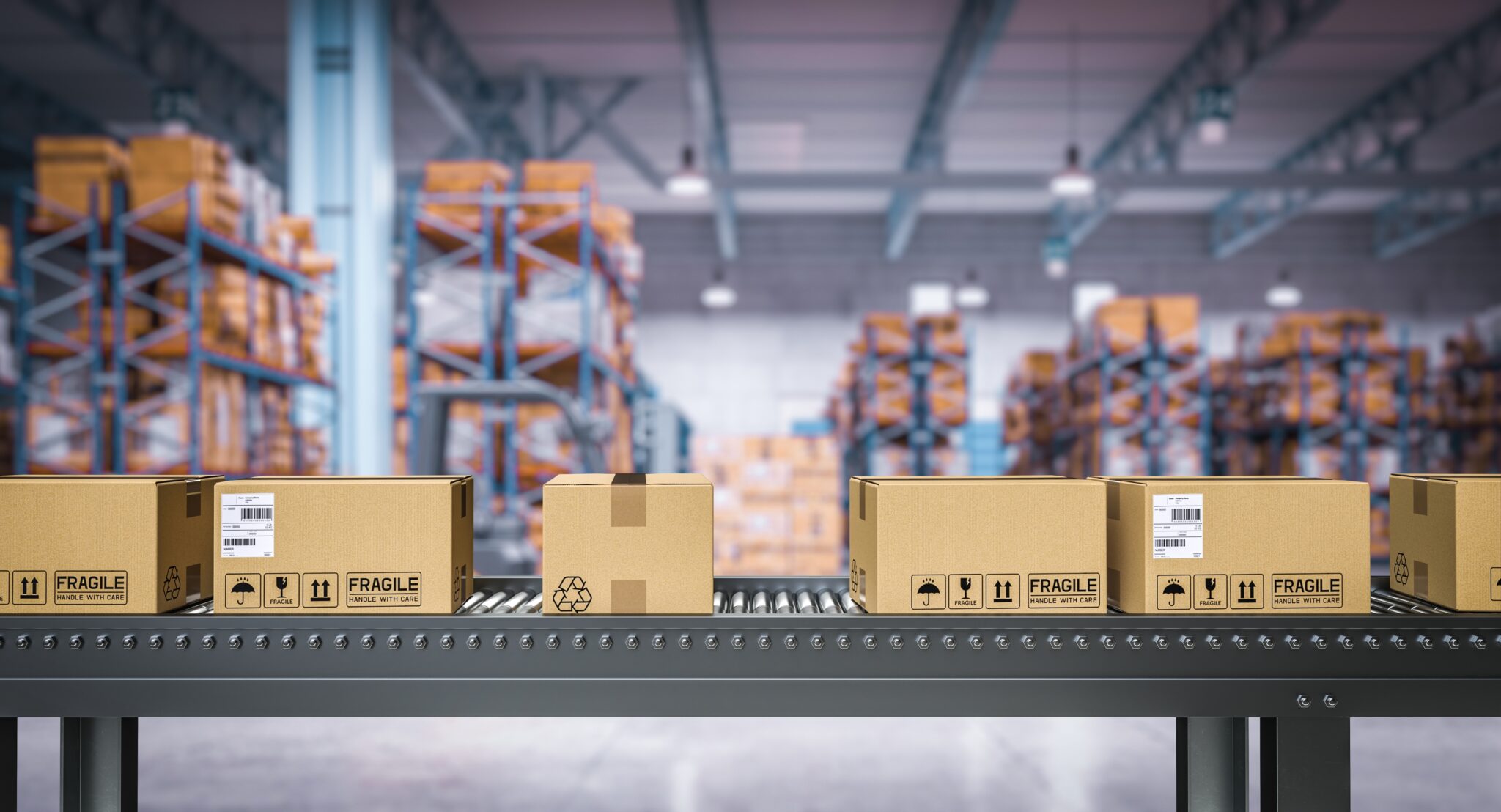
Logistics Cost Allocation
Logistics Cost Allocation
This was precisely the challenge facing DHL Express several years ago, according to Robert Jordan, Founder and CEO of The Information Factory. “A few years ago, DHL reviewed its costing approach with a view to ‘turbocharging’ it, ” Jordan explains. “DHL, being extremely customer-focused, approached it from the customer end. They wanted to get customer profitability sorted, because they discovered many customers were engaging them for services that weren’t profitable.”
Read the full story now
The fundamental question was simple yet profound: How do you accurately determine profitability? Traditional costing methods based on the previously mentioned largely estimated calculations had led to the creation of an environment where stakeholders didn’t fully trust the cost data they were seeing. “Someone clever in finance insisted that the costing had to reconcile to the general ledger,” says Jordan. “They took the general ledger and said, ‘these are our costs because we know what they are.’ It has to absolutely reconcile to the general ledger.”
The result was a shift to Activity-Based Costing (ABC), initially implemented as what Jordan describes as a “black box” system, namely opaque, difficult to understand and hard to modify. The Information Factory’s mandate was to replace this with a transparent solution offering clear visibility into costing rules and their application, along with the ability to refine these rules over time.
read all our eBooks here.
similar news