Operational demands can be better met by integrating service logistics, writes Scott Allison (pictured below), Chief Customer Officer, DHL Supply Chain.
Manufacturers have spent the last decade trying to find the balance between cost-effective inventory management and security of supply to ensure product availability and avoid downtime, poor customer service, or outages. But by integrating service logistics into a supply chain strategy, businesses can find the balance between the two, achieving a more cost-effective route to getting the right product, in the right place, at the right time.
The swinging pendulum
Maintaining optimum inventory levels has been one of the biggest challenges for almost every industry for the last four years, no one can afford the downtime or damage that can result from the absence of a critical component.
But in today’s economy, ‘availability at any cost’ isn’t a viable option. Holding inventory for every eventuality has become prohibitively expensive as real estate and labor costs escalate. An audit of one semiconductor company’s supply chain infrastructure revealed that 54% of its inventory, housed in high-cost markets Singapore and Silicon Valley, hadn’t moved in a year. Beyond the cost barrier, companies that hold too much inventory can also become less responsive to shifts in market demand or changing customer needs. Their ability to adjust their offerings becomes constrained by the large amounts of stock they need to sell or manage.
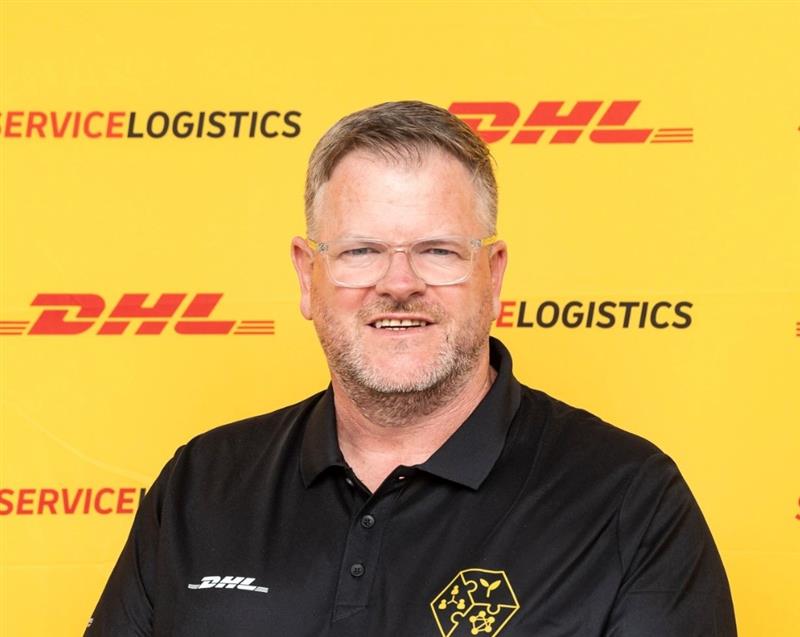
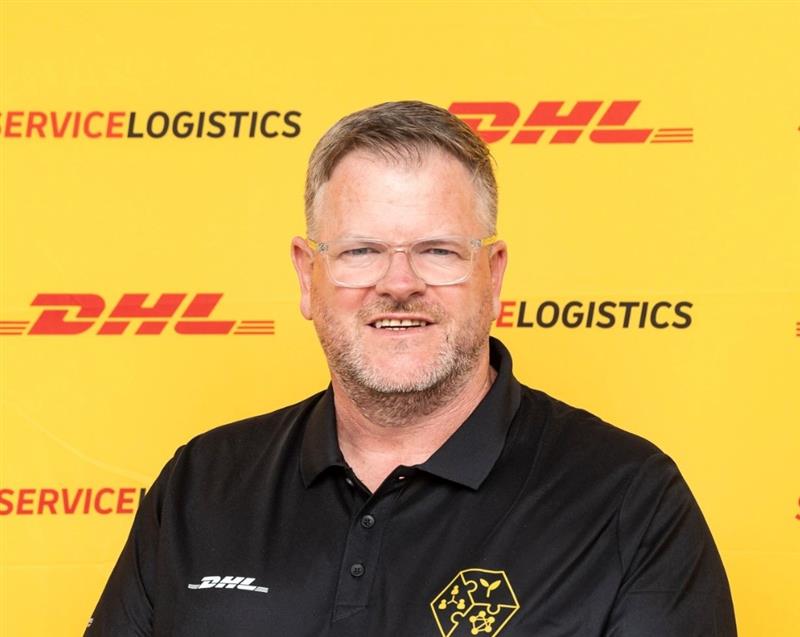
Scott Spain
Despite the need for surety of supply, when times are tough there’s a risk that businesses will revert back to ‘just in time’ supply chains that come with high risk. Service logistics sits at the centre of this challenge – an agile service part network ensures the right goods are close to where they need to be without the expensive overheads thanks to technology, access to a wide network, fulfillment expertise, and effective supply chain planning.
Going back to network design
To increase supply chain flexibility and meet critical operational demands, businesses will benefit from analyzing network flows and processes to create strategic and tailored supply chain designs.
As businesses grow, it’s common for supply chains to expand in a fragmented way, rather than as one ecosystem. By centralizing data and creating cross-functional processes, teams will be able to ensure they can work in alignment, improving operational efficiency and reducing bottlenecks. Improved access to data and digital tools will help to optimize the organizational structure, as well as improve a company’s understanding of its products and operational performance. This will allow organizations to map stock volumes and locations closer to the point of demand, improving fulfillment, repairs, and returns needs. In the wake of global disruption, network design is central to maintaining reliance and ensuring businesses can continue to deliver, even in times of supply chain strain.
Maintaining consistency with technology
In the semiconductor industry example, a company holding excess stock, we approached their issue with advanced industry visibility tools, providing understanding into why certain parts remained in stock. As a solution to better manage stock and inventory, we supported in setting up a new operation in a cheaper real estate market, which resulted in over £3.5M per year in savings.
In another example in the PC & Laptop industry, we were able to improve the turnaround time of returned stock by 40% using AI-recommended disposition logic, which had a 99.7% first time right assessment.
In today’s unpredictable environment, service logistics can give businesses the assurance and stability they need to keep operating and serving customers, while maintaining operating costs.
similar news