Integrating racking systems, pick towers and other storage solutions with mobile robots will provide transformative automation, says Edward Hutchison, Managing Director of BITO Storage Systems.
Fast delivery times and flexibility are vital warehouse capabilities for meeting customer expectations, especially in the intensified environment of e-commerce fulfilment during seasonal peaks. The traditional solution of adding more staff is becoming increasingly difficult as it becomes harder to find and retain qualified labour. And if you can find more people, order picking operations that involve long walking distances will increase costs.
Autonomous Mobile Robots (AMRs) are fast becoming a familiar sight in warehouses. They offer a flexible automated solution that negates the need for extensive modifications to facilities. They can adapt easily to seasonal demands as extra robots can be added as required, providing an ideal solu¬tion for handling peaks. And when business circumstances change, operations can be further extended by simply adding robots to the fleet.
This versatility along with their performance possibilities is driving a 12.6% AMR market growth in the UK from 2024 to 2030. Many of the projects will be part of a broader storage installation and may well be working with racking and shelving.
In addition to e-commerce, mobile robots are also suited to sectors such as fashion, food and pharmaceuticals. They can be particularly useful for automating small item order picking, where collaborative robots under the direction of intelligent control software create more efficient, flexible and productive processes. Robots can double or even triple productivity levels by reducing travel times through intelligent routing, optimising processes through batch picking and increasing picking performance through zone picking. The number of order pickers can be reduced by up to 50% and processes can be optimised in the long term by allocating staff to other value-adding tasks.
When it comes to installations, integration can be performed while maintaining ongoing operations. Solutions can be adapted to a user’s existing storage installations such as pallet racking, shelving and multi-tier storage systems, with a flexible connection to existing WMS/ERP systems.
Compared with other forms of automation, investment in mobile robots is small as they do not require any supporting infrastructure and operations can start with a single unit then add others as required. This is helped by the flexible Robot-as-a-Service (RaaS) licence model offering reasonable prices, which also enables simple fleet scalability, with the short term addition of units to handle seasonal peaks.
Transformative materials handling
Well planned racking layouts providing narrow aisles will give robots access while maintaining storage density and allow picking routes to be optimised. The structures will require labelling and clearances to allow a mobile robot’s sensors to navigate effectively.
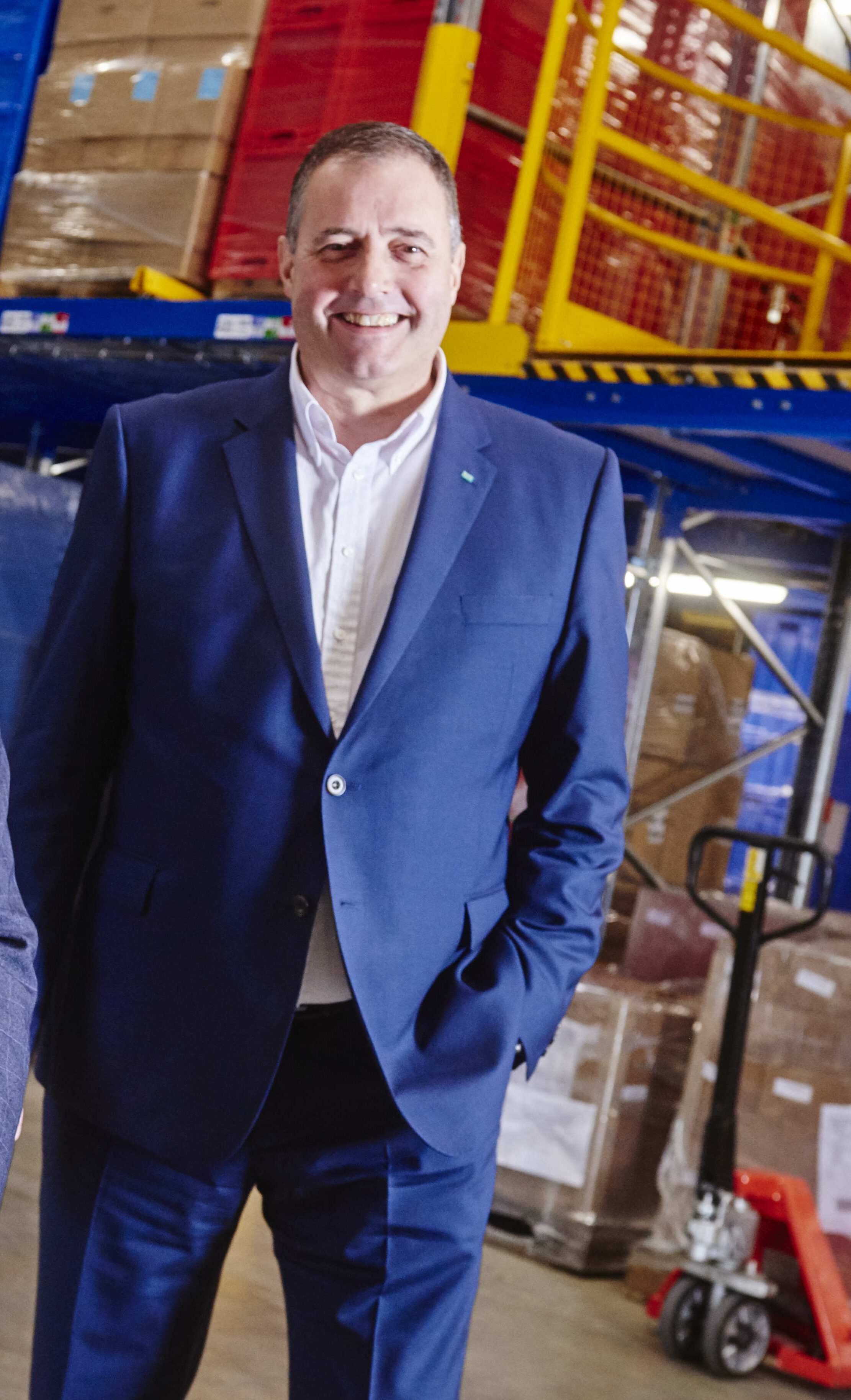
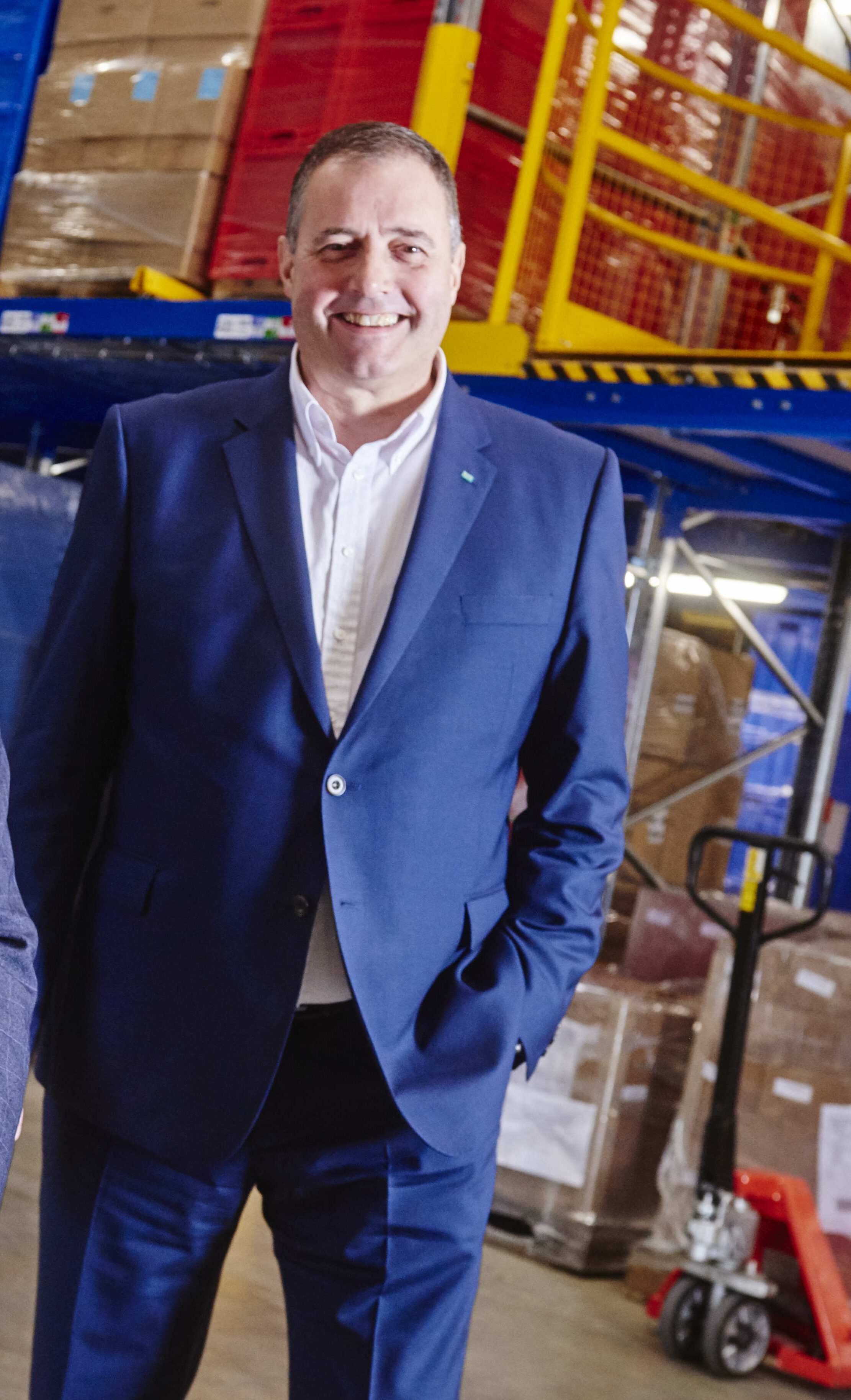
Edward Hutchison
Integrating BITO’s racking systems, pick towers and other storage solutions with mobile robots will provide transformative automation that is seamlessly integrated, error-free and deployed without operational disruptions to meet the demands of a rapidly evolving logistics landscape. When choosing a mobile robot, look at the min¬im¬um space re¬quire¬ment. An ability to work in aisles as narrow as 1.12 m will enable use in confined storage environments. Another key characteristic to consider is charge time, which is an important contributor to overall productivity. Short charging times of just 50-60 minutes will help towards uninterrupted operation.
One stop shop suppliers will make the most effective partners to provide complete robot and materials handling solutions that will be transformative for warehouse operations. In addition to providing its own LEO driverless transport system, BITO works with numerous suppliers of mobile robots to provide innovative storage and order picking solutions, which may also involve shelving and racking installations such as pick towers, as well as plastic totes and containers. This allows customers to design and implement future-proof, end-to-end warehouse solutions, integrating state-of-the-art storage systems with robotics-powered automation to create smarter, faster and more efficient supply chain operations.
similar news