Warehouse automation is your best defence against supply chain chaos, writes Mats Hovland Vikse (pictured), Chief Executive Officer of AutoStore.
Since 2020, supply chains around the world have been pushed to their limits. From pandemic lockdowns and overloaded ports to conflicts overseas and heightened geopolitical risks, businesses have faced the perfect storm of disruption. On top of that, economic challenges like inflation, fluctuating interest rates, and changing trade policies are driving supply chain executives to rethink their approach – not just to streamline their operations, but to build lasting resilience.
In this volatile environment, automated warehousing solutions have become a game-changer. What was once primarily about speeding up processes now serves as a critical foundation for navigating uncertainty, safeguarding service quality, and enabling businesses to pivot quickly in today’s unpredictable world.
How Supply Chains Are Evolving
Global disruptions continue to reshape how businesses manage their operations, forcing a fundamental shift in supply chain strategies. In light of recent U.S. tariff changes – including a new trade agreement imposing 15% tariffs on European exports to the U.S. – many companies are shifting away from “just-in-time” inventory models in favour of “just-in-case” approaches.
In fact, nearly a third (28%) of industrial manufacturing supply chains have or are planning to move production closer to end markets. Stockpiling inventory domestically ahead of potential tariff increases has become a widely adopted tactic – creating a pressing need for increased storage capacity and greater warehouse density, challenges that traditional warehousing struggles to address efficiently.
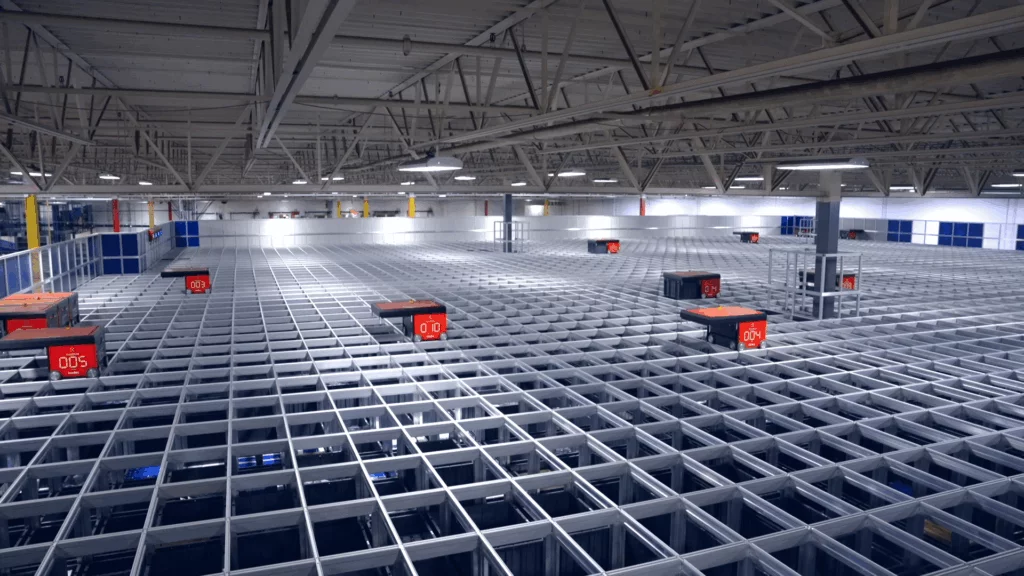
At the same time, labour shortages in the warehousing sector are intensifying. High turnover rates and lengthy onboarding processes add operational strain, making it difficult for businesses to maintain consistent service levels. To overcome these hurdles, companies are turning to automation solutions that minimize reliance on manual labour while delivering scalable, reliable performance.
Driving Resilience Amid Uncertainty
Automation has become more than just a productivity booster – it’s a vital strategy for cutting costs and building resilience. Gartner highlights that companies turning to automation are positioning themselves to navigate uncertainty and maintain a competitive edge.
Automated storage and retrieval systems (ASRS) are at the forefront of this shift. These solutions dramatically increase storage capacity within existing warehouse spaces and offer the flexibility to scale throughput up or down based on fluctuating demand. This adaptability is crucial for implementing a just-in-case inventory strategy, allowing businesses to keep more products closer to customers and respond quickly to sudden demand surges or supply chain disruptions. In short, automation transforms warehousing from a static cost centre into a flexible, resilient engine for growth.
The pandemic served as a clear dividing line. Organizations that had already embraced automation – leveraging ASRS, goods-to-person (G2P) technologies, and agile warehouse management systems – were able to ramp up order fulfilment and manage labour shortages with far greater ease than those relying on manual operations. This experience has solidified automation’s role as a foundational driver of warehouse efficiency and business continuity.
Automate Now To Thrive Tomorrow
Uncertainty isn’t a temporary challenge, it’s the new business climate. Between ongoing global disruptions, rising logistics costs, and ever-increasing customer demands, supply chains are being stretched to their limits. For leaders navigating this landscape, standing still is the biggest risk of all.
To stay competitive, companies must now assess their level of automation to optimize costs, boost productivity, and build resilience. Postponing this decision doesn’t just delay progress – it risks entrenching inefficiencies that become harder and more costly to unwind over time.
Traditionally, warehouse automation came with steep upfront capital requirements, placing it out of reach for many. That paradigm is shifting. Flexible, as-a-service models are breaking down those barriers and accelerating adoption across the industry. These models allow businesses to pay for what they use, adjusting storage and throughput as needed. With no large capital outlay and all-inclusive pricing that typically covers maintenance and integration, businesses gain immediate access to automation without the financial strain.
Crucially, this model allows for dynamic scaling. Companies can adjust capacity in real time to meet demand, avoiding the risks of overbuilding or inventory shortfalls. The result? Reduced financial exposure, faster ROI, and greater control over their operations.
In a climate where disruption is constant, warehouse automation is no longer a nice-to-have – it’s a strategic imperative. It offers not only protection against uncertainty but also a platform for long-term growth and adaptability.